Traditionally, two different centering systems are used when closing an injection mold: four guiding pillars placed at its corners ensure a rather coarse pre-centering during the initial stage of the closing movement, while during the last millimeters of the course, four additional flat centering devices on the sides of the mold ensure the fine centering. Is it really necessary to have two systems that do not harmonize optimally? An interview with the head of mold maintenance at connector manufacturer Stocko Contact about his experience with the high-precision, single-stage Agathon Guiding System Plus.
«We are a manufacturer of connector systems for industrial sectors such as household appliances, heating technology and the automotive industry», says Oliver Müller, Head of Tool Service at Stocko Contact GmbH & Co. KG in Hellenthal (Germany). Connection to the wires is performed using different technologies such as insulation displacement, crimp or solder connections. Stocko relies on proven solutions, high quality and a wide range of applications. In the face of sometimes much larger competitors, the company relies above all on innovation, flexibility and development partnerships to find solutions to new challenges on the market. Increasing functional density and miniaturization of the devices result in dwindling product life cycles of existing articles. Hence, customers increasingly require individual adaptations or new developments. To satisfy these demands, Stocko relies on the expertise, vision and pragmatism of its designers to develop solutions that are both technically feasible and economically viable.
Increased requirements on production tools
«These higher demands on the products can only be met with the help of correspondingly powerful tools,», adds Oliver Müller. This applies both to the progressive tools used in the production of stamped parts and to the tools used for injection molding. While the progressive tools are mainly sourced externally, the injection molds are manufactured in-house. They are extremely complex and consist of hundreds or even thousands of individual parts. Many of these are very filigree. To ensure that the connector housings produced with these tools function perfectly, the molds must be manufactured with the utmost precision. For their production, Stocko thus relies on the best available state-of-the-art technology. This also applies to the standard components that ensure the essential functions of the mold, such as the high-precision closing movement. Even the smallest deviation during centering can lead to misalignment or burrs on the components and thus to rejects. The long-term behavior of the centering and guiding elements also plays an important role, as the molds must sometimes withstand several million production cycles. The expenditure for maintenance and servicing is therefore a significant factor. This also applies to progressive dies.
Agathon Guiding System Plus instead of flat guides
«In injection mold-making, two different systems are traditionally used to guide and center the mold halves during closing: guide pillars and flat guides», says Matthias Rüter, Area Sales Manager at the German branch of the Swiss precision parts manufacturer Agathon in Bellach (Switzerland). The guide pillars at the corners ensure the coarse alignment at the start of the closing movement, while four flat guides in the middle of the sides of the mold ensure the fine alignment over the last few millimeters of the closing stroke. The relatively short working distance of the flat guides can lead to undesirable metallic contact in molds with narrow spacing and strongly inclined contour sections, which can have detrimental effects on the product. Another disadvantage is the wear that occurs on the flat guides due to the high surface pressure, which can also result in damage to the sliding surfaces. In the case of long-running molds, the flat guides may even have to be replaced several times over the lifespan of the tool.
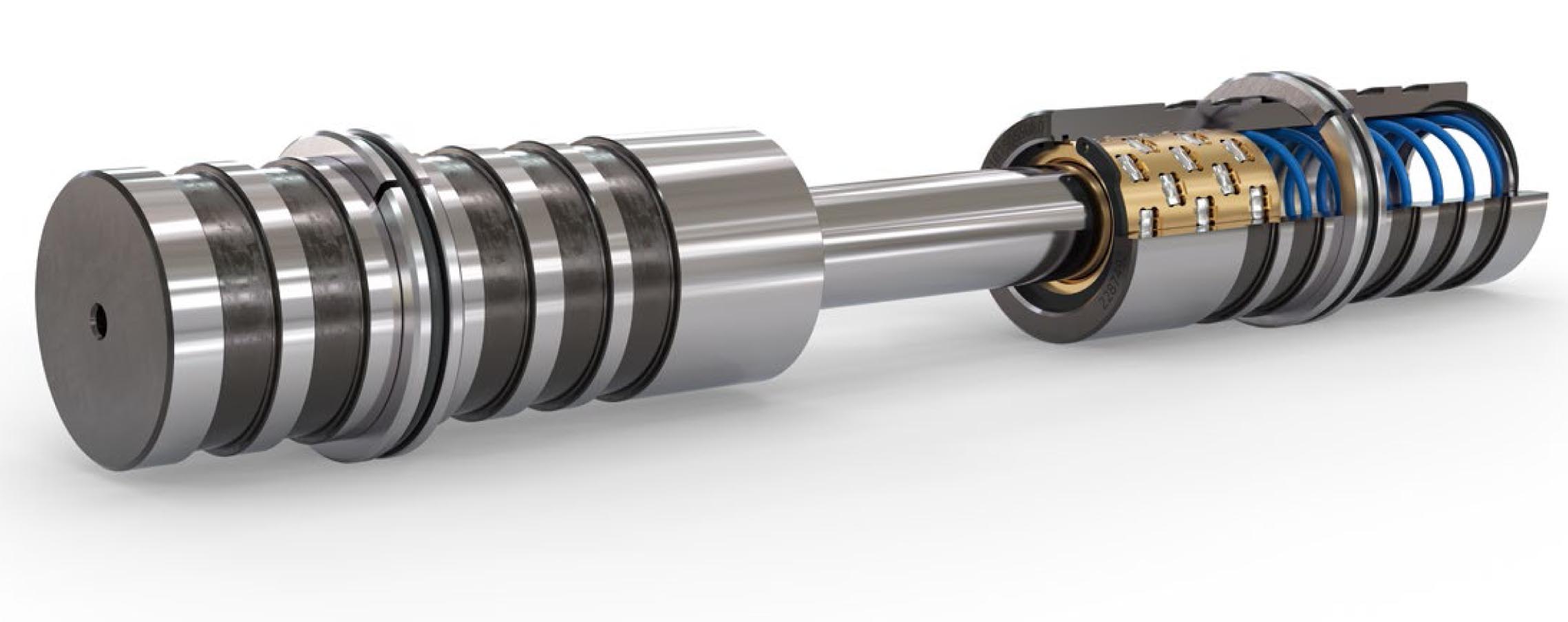
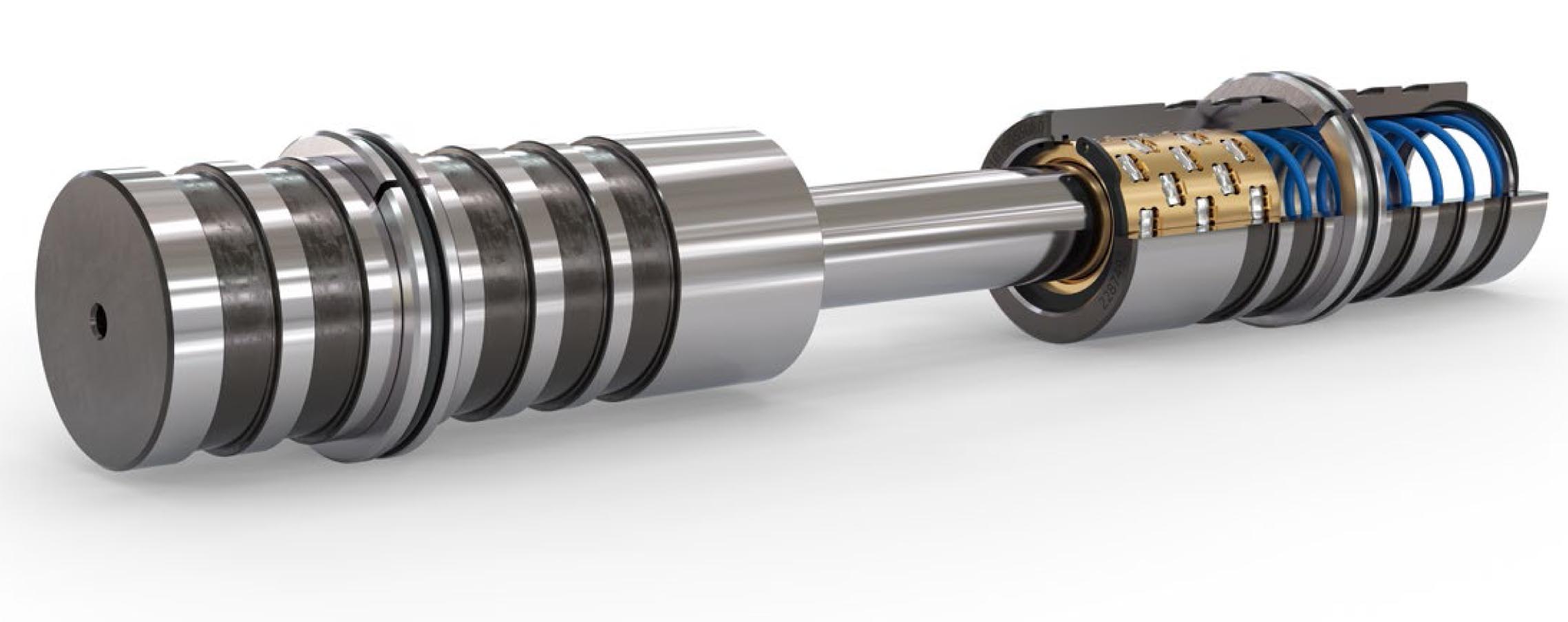
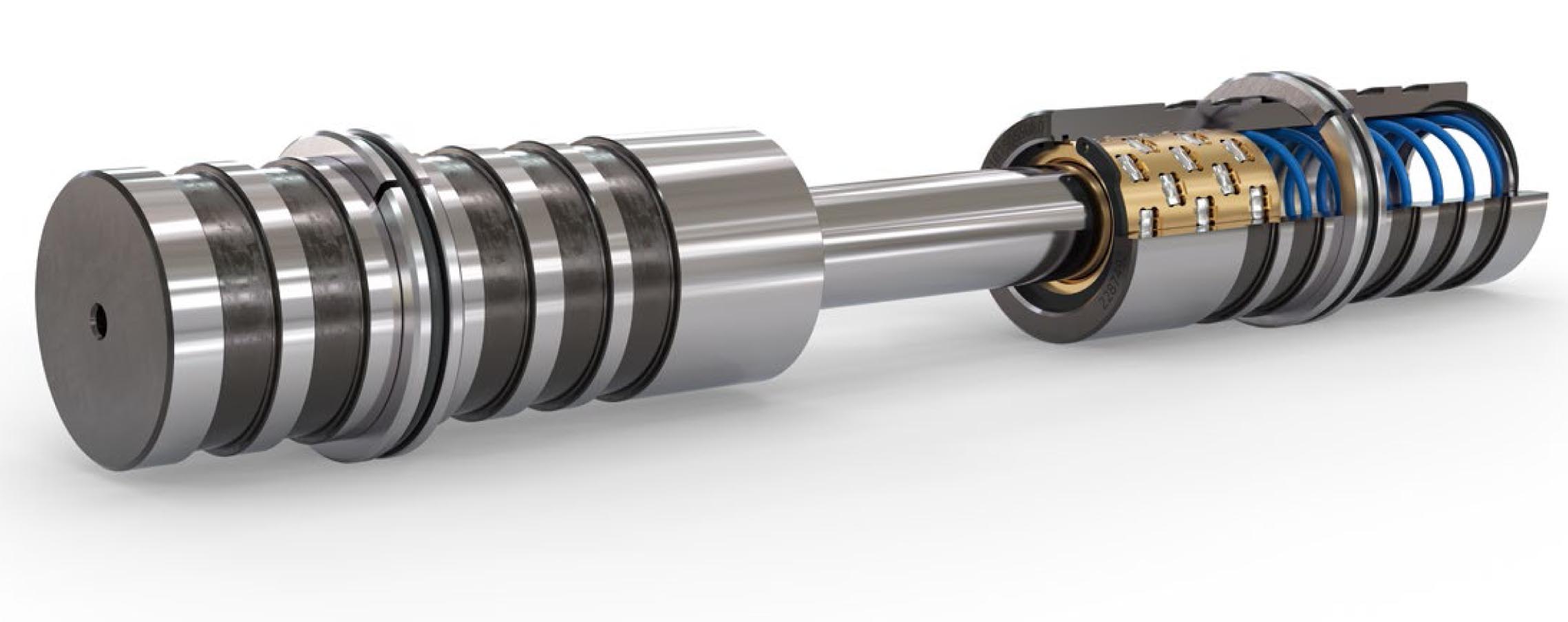
Agathon has therefore developed the Guiding System Plus as an alternative. This consists of long precision-ground guide pillars with tolerance h3 at the four corners of the mold, which glide into matching roller cages with high-precision rollers on the opposite half of the mold. The guide pillars, cages and rollers are manufactured with such precision that the guides operate with zero-clearance as soon as they enter the first row of rollers. Thanks to their linear contact with the guide pillar, the rolling elements have more than 6 times the load capacity and rigidity of a ball pillar guide. The mold halves are thus guided with maximum precision over almost the entire length of the closing stroke. Another advantage is the smaller “footprint” of this "two-in-one" solution compared to the traditional approach. The resulting omission of the space required for the flat centering elements allows additional cavities to be accommodated on the same surface area. Alternatively, a smaller mold can be mounted on a smaller machine while offering the same production capacity.
Outstanding durability
«In 2021, we decided for the first time to use the Agathon Guiding System Plus for a mold for stove connector housings that we were having problems with», reports Oliver Müller. As there was already a long-standing partnership with Agathon in the field of high-precision guiding systems for progressive tools, it was obvious to take a closer look at Agathon's new development for this injection mold as well. In the past, the flat guides on this mold had to be replaced after around 625,000 injection cycles due to increased wear damage. This was partly also attributable to the particularly high mold temperature of 140 °C. The previous flat guides and guide pillars were replaced with four Agathon Guiding System Plus after 2.5 million cycles. With the new system, the mold has since completed a further 1.5 million injection cycles without any complaints in the area of the guides.
Unfortunately, the connector model produced with this mold is to be discontinued in the foreseeable future. Therefore, in this case there will probably be no chance to get close to the actual durability limit of the Agathon guide. However, based on the experience gained to date, he could envision that the maximum number of cycles that could be achieved might be in the double-digit million range. As the Agathon guide costs hardly any more than the original equipment, the investment has more than paid for itself, if only because of the two sets of flat guides that have been saved so far. In addition, the higher availability of the mold and the injection molding machine would also be a bonus, as the Agathon Guiding System Plus, unlike the flat guides, no longer needs to be lubricated daily, but only once a week. In addition to the higher availability, this also saves the reject parts produced during the usually 5-15 start-up cycles that are required after such shutdowns.
Based on this positive experience, around 15 sets of these mold guides have now been installed in other molds. The experience with these conversions has also been positive. The centering devices proved to be easy to handle, durable and required little maintenance. In the case of molds that are used for shorter times, he assumes that the removed Guiding Systems Plus can be easily reused in other molds when the first tool is taken out of service. In the area of mold maintenance, employees have commented positively that the smooth separation of the mold halves makes work much easier and that the soft-face mallet and assorted lever assembly need to be used much less. The required minimum quantity of lubrication can also be performed easily.
Good marks for the service
«I can also give Agathon a good rating in the area of support and assistance», says Oliver Müller, summarizing his experience. In the event of questions or problems, there was always prompt support, whether by telephone, in a teams meeting or through a short-term on-site visit by the field service. Compared to his experiences with other suppliers, this is far ahead of the others. Not only from a technical, but also from an economic point of view, it is worth considering making Guiding System Plus a standard feature when making new injection molds.
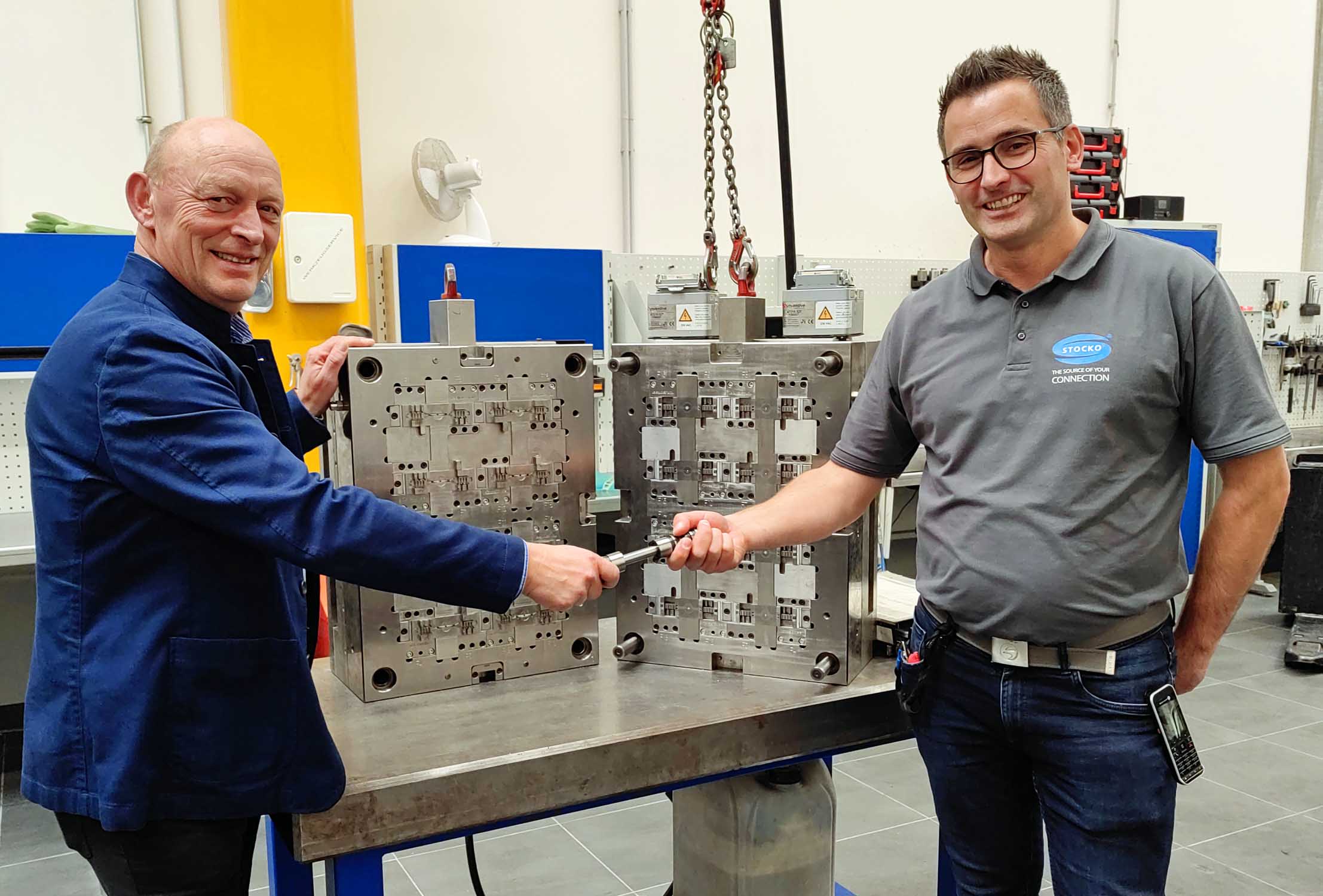
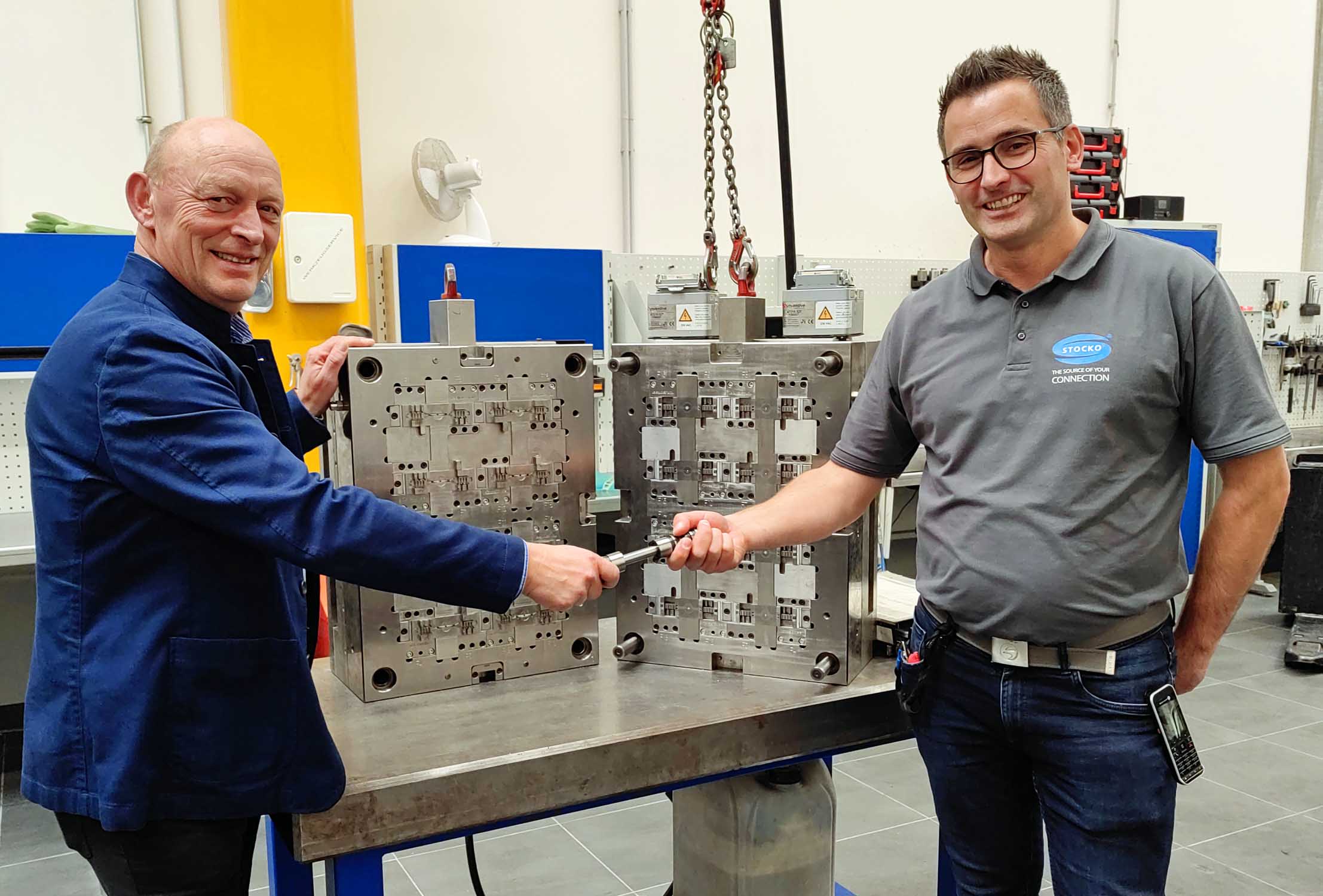
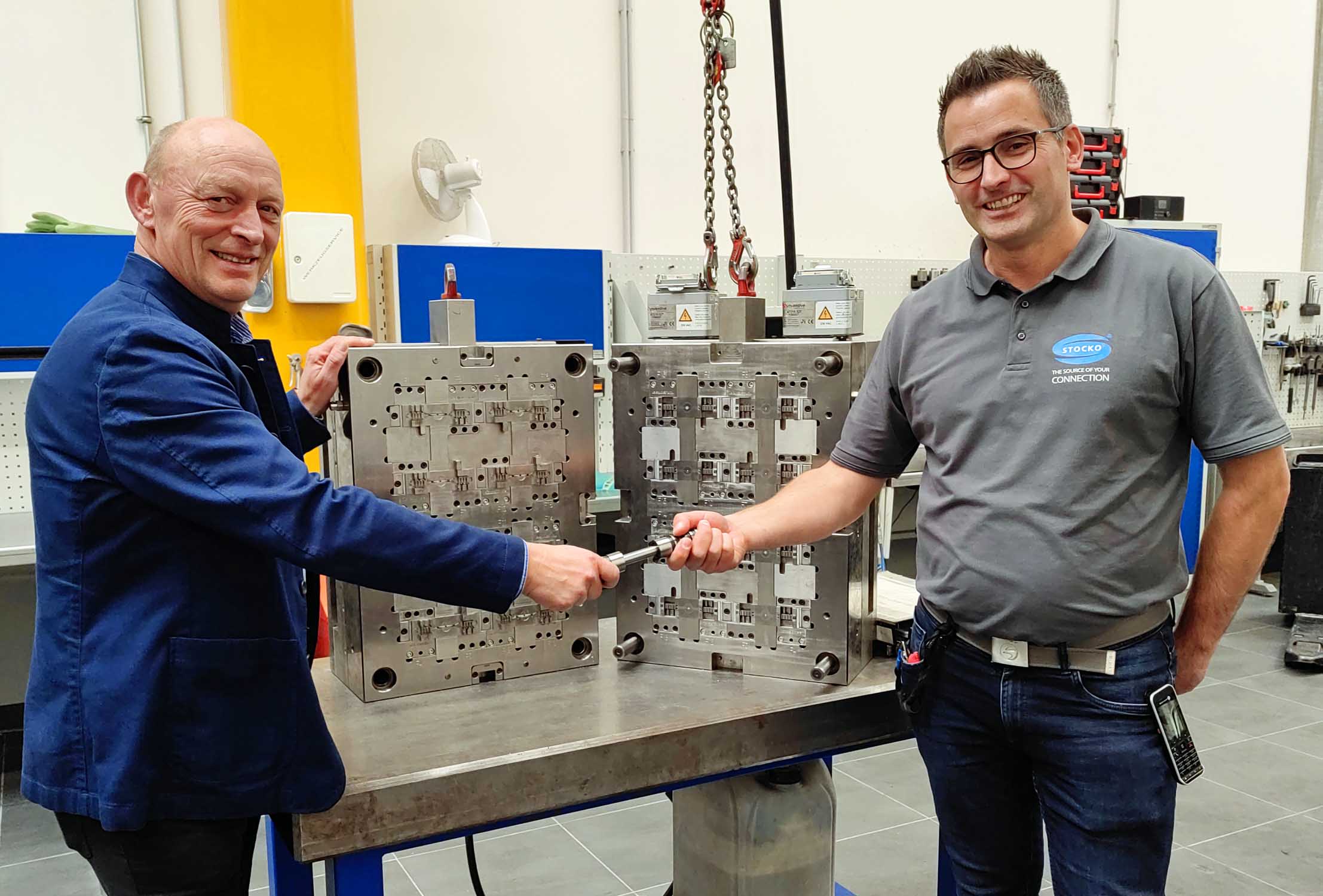
The monitoring of the production and maintenance of the molds in the mold-making shop itself and the linking of their operating data with the data from production is performed to a very large extent, resulting in huge amounts of data. The outcome is a very high degree of control over the ongoing production processes. «Based on my experience in the industry, I can confirm that the level of production data acquisition at Stocko Contact at plant level is exemplary,» says Matthias Rüter.
Agathon – Strive for the best