What benefits does the laser processing provide? The combination of laser roughing and grinding is the most efficient way to machine indexable inserts with tips made of superhard materials.
Agathon has always insisted on this since the introduction of its Neo laser processing machine. Here is the evidence.
One thing is clear: the laser has become indispensable in the processing of superhard materials such as polycrystalline diamond (PCD). Its speed and cost advantages over grinding are obvious. But how exactly should the laser be used? And how exactly can the advantages mentioned be quantified? These are questions to which the Swiss manufacturer of laser processing and grinding machines provides further answers.
About the process: PCD is hard, very hard. This makes indexable inserts with PCD tips extremely wear-resistant. For this reason they are gaining popularity in the machining of carbon fiber reinforced plastics (CFRP) for example. PCD is so hard that grinding indexable inserts with PCD tips to the final contour is a complex process in two aspects: firstly, the grinding process takes a long time, because diamond is machined with diamond. Secondly, the process is expensive for the same reason. A few years ago, a new process emerged on the market to machine workpieces with an ultra-short pulse picosecond laser and bring it to its final shape. With such a laser, material can be removed without thermally damaging the rest of the material. The fact that high-precision cutting edges can be produced in this way sounds promising. The process is extremely slow and highly complex, still it is clearly inferior to grinding, especially when machining tungsten carbide.
Agathon’s engineers have therefore decided to combine the best of both worlds; the non-cutting and the metal-cutting worlds. The result is the Neo laser processing machine, with which the PCD tip, including the clearance angle, is first removed to the final contour down to a few hundredths of a millimeter. The workpiece is then given its final shape with a grinding machine – ideally with an Agathon grinding machine. This is because the products of the Swiss machine manufacturer not only work with the precision required for this, but also provide the process engineering prerequisites required for the machining of superhard materials, such as in-process dressing and very high static stiffness.
As precision is achieved in the subsequent finishing process, the main focus can be placed on the speed of the pre-processing of the workpiece, laser roughing. For this reason, the Neo uses a nanosecond laser which light pulses are longer than those of a picosecond laser. In this way, it introduces more energy into the workpiece, so that more material is removed, therefore the process is greatly accelerated. In specific terms, the PCD removal rate with the Neo laser processing machine is 10 mm3/s meaning 100 times higher than in the typical grinding process with a removal rate of 0.1 mm3/s.
Laser + grinding is better than just grinding
Now let’s consider the advantages of the Agathon-designed combined process of laser roughing and ground finishing compared to grinding using the grinding machine alone. Three resources can be economized on: firstly time, secondly abrasive rim and thirdly dressing rim. Basically, the more work the laser processing machine takes over from the grinding machine, the less time is required and the less the rims wear to process the carbide support and PCD tip to the final dimension. This means that the specific savings depend on two factors: on the one hand, the dimension of the PCD tip and, on the other hand, how close the laser roughs to the final contour.
The size of the PCD tip stock removal after it has been soldered onto the carbide support, depends entirely on the user’s individual processes. If the PCD blanks are eroded in order to divide them into individual tips, the stock removal, for example, is considerably higher than 200 µm, because the surface of the PCD is structurally altered to a certain depth by eroding. The decision as to how near to the final dimension the Neo laser processing machine should roughen is just as individual. Although the heat-affected zone of the laser used in the Neo is smaller than 5 µm, but in order to ensure a stable grinding process the stock removal after laser roughing should be between 20 and 30 µm.
Agathon has conducted a series of tests to find out how much time is needed to bring the insert to the final size. How much wear there is on the grinding and dressing rims depends on the different stock removals. From this data, the user can determine how much time, material and money he saves, if he prefers laser roughing to the grinding process. From this he can calculate how long it would take to amortize the investment in a Neo laser processing machine.
For the tests a ceramic bonded D10 grinding wheel with a diameter of 250 mm and a width of 12 mm was used, which was mechanically conditioned in the process with a high-grade corundum cup. A single-sided diamond-shaped indexable insert (VCGW 160408) with an inscribed diameter of 9.52 mm was machined. The PCD tip had a final dimension of 4.9 mm edge length and was 0.5 mm thick. Roughing was performed on the Neo laser processing machine and grinding on a Leo Peri grinding machine.
Looking at the measured data and their progressions, it can be seen that both the process time and the wear increase almost linearly with the increase of the stock removal. This linear increase facilitates the calculation of the results for those values that were not specifically included in the measurement series. In all measurements, the measurement after soldering was 400 µm per side. In three measurement series, this measurement was reduced with the laser to an average of 67, 41 and 24 µm per side. Ten indexable inserts were machined in each of the three measurement series.
The data are self-explanatory
Without an up-front laser machining process, the grinding machine required 520 s to process indexable inserts with 400 µm stock removal to the final dimension. If, on the other hand, the stock removal was roughened to 24 µm with the laser, the grinding machine reached its target within an average of 240 s. The processing time on the grinding machine was reduced by 280 s, i.e. 54 %. Taking into account the 60 s required by the laser for roughing, the total process time still saved 220 s or 42 %. With a stock removal of 41 µm, the time saving on the grinding machine was 255 s or 49 % and for the entire process 195 s or 37.5 %. After all, a respectable 240 s or 46 % for grinding and 180 s or 34.5 % for 67 µm stock removal, the time saving was still a good 240 s or 46 %.
The wear values are just as spectacular. On the grinding wheel, the rim was worn by 0.067 mm when the total stock removal of 400 µm was ground. Only 0.025, 0.023 and 0.02 mm were measured with a stock removal of 67, 41 and 24 µm. This corresponds to a reduction of 63, 66 and 70 %. The wear on the rim of the dressing cup was reduced from 0.274 mm to 0.128, 0.122 and 0.118 mm. This in turn means a reduction of 53, 55 and 57 %.
«These are, of course, values that can certainly motivate insert manufacturers with tipped inserts to invest in a Neo laser processing machine », says Agathon CTO Dr. Stephan Scholze. For him, these figures confirm what the company has always pointed out: the combined process of laser roughing and grinding finishing on the grinding machine is the most efficient way to manufacture indexable inserts with superhard tips to final dimension.
Authors:
Josquin Pfaff, Process engineer Agathon AG
Lars Henzi, Application engineer Agathon AG
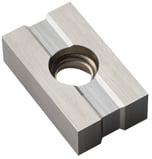